Cylinders aren't the only thing we're known for.
Clients know us for our superior quality, excellent customer service, and on just-in-time deliveries.
T-Mac Cylinders, Inc. formed in 1996 to provide customers with these three key elements required in this industry today, and to expand on these in the 21st century.
T mac free download - WinZip Mac, Avast Free Mac Security, AVG AntiVirus for Mac, and many more programs. T-Mac Sports Shirts T-Mac Sports Hoodies T-Mac Sports Hats MINI HELMET VISORS. 6 Visor Types, Infinite Possibilities. UA MINI CLIP SPACERS. Works with all UA Mini Clips. High School Mini Helmets. More than 600 Schools, we are the go to place for the most accurate HS Mini Football Helmets around. Mini Award Decals. TMAC measures tool wear and detects breakage in real-time by monitoring true spindle motor power. TMAC learns the optimum power for each tool and cutting section, and compares it to the user defined limits to calculate wear as the tool is cutting. TMAC has developed a Hazemeyer Earthing System allowing the user to isolate each earth individually to conduct repairs and testing, while still maintaining safety. DNOB When line crews attend a site, they cannot begin work until the link switch is open and the Do Not Operate Banner (DNOB) is applied to the power lines.
At T-Mac Cylinders we strive for no less than the best. The quality in our cylinders is in machining,
performance, and aesthetics. Look at our design features. Honed aluminum tubing with closer ID tolerances than drawn tubing. Precision ground end caps for precise machining control, giving you true and square cylinder mounts to extend the life of your cylinder. Low friction to extend seal life. These and the additional features listed herein, along with our stringent quality control process, means you as a valued customer receive T-Mac Cylinders with quality second to none.
We are in business to serve you. It's that simple. We know circumstances arise that require special attention. Flexibility is a must in this industry. We cover your needs in emergency situations, expedite to meet your customer demands and find solutions for the most unique scenarios. Our policy is to do everything in our power to meet your needs.
We manufacture NFPA Aluminum Air & Hydraulic Cylinder and are a global distributor based in the USA and follow NFPA for standard, custom air and hydraulic cylinders. Awesome screenshots chrome extension for mac.

INTRODUCING TMAC VERSION 3.0!
Caron Engineering's new adaptive tool monitoring system has a browser based user-interface for remote access to live monitoring and system control from any network connected device. Check out all the new features of TMAC 3.0! (Short Video)
Optimize Machine Tool Cutting
TMAC uses high-resolution sensor data to measure tool wear in real-time. Through direct interfacing with the CNC control, TMAC makes automatic and instantaneous corrective adjustments during cutting, without the need for human intervention.
TMAC maximizes your investment in the entire machining process through optimization and the elimination of downtime, resulting in more profitability.
Real-Time Tool Wear Detection
TMAC measures tool wear and detects breakage in real-time by monitoring true spindle motor power. TMAC learns the optimum power for each tool and cutting section, and compares it to the user defined limits to calculate wear as the tool is cutting. It operates on the principle that the power required to cut a part increases as the tool's cutting edges deteriorate.
- Monitors and reacts to tool wear in real-time
- Uses multi-range sensors with auto-scaling display sensitivity
- Prevents tool breakage and lowers scrap rate
- Reduces the cost of consumable tooling
- Provides valuable information about the cutting process
- Stops the machine instantly in the event of tool breakage
TMAC learns the peak power and area under the curve of the cutting tool and can detect tool wear by monitoring these parameters.
- Auto-Scaling Display
- Fixed Limits
- Work (Area Under the Curve)
AUTO-SCALING DISPLAY
TMAC learns the cut and automatically scales the display to the ideal monitoring range, for optimum sensor resolution.
FIXED LIMITS
- TMAC learns the peak power of the cutting tool
- Alarms can be set for extreme (red), wear (yellow), and undercut (blue) per tool
- TMAC will finish the current cut when a wear limit is reached and safely expire the tool after cutting
- TMAC will immediately stop the machine and retract the tool when an extreme limit is reached
- Undercut limits can be set to alarm if not enough power was achieved based on the learned value for the cut
WORK PERCENTAGE (Area Under the Curve)
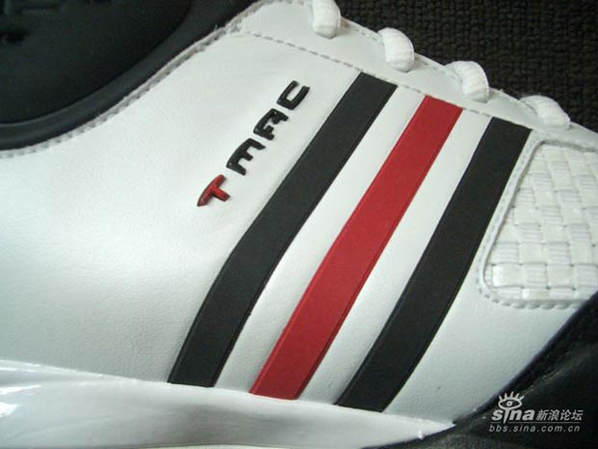
- With work, TMAC is measuring POWER OVER TIME to calculate the total power consumed over the duration of the cut
- As the tool gets dull, more power is used, so the area under the curve will increase and eventually reach a wear limit indicating a tool change is required
Reduce Cycle Time with Adaptive Control
CNC machines are typically programmed for the safest feed rates to accommodate the worst machining and material conditions.
TMAC adaptive control learns the optimum power for each tool and continuously maintains a constant tool load by automatically adjusting the feed rate in real-time. The result? Decreased cycle time, longer cutter life, and more machine uptime, especially with difficult to machine materials.
- Typical cycle time savings of 20 – 60%
- Allows tools to run at optimum feed rates
- Adjusts to variations in material, tooling, and depth of cut
- Excellent for unattended/lights-out operation
- Adjusts feed rates smoothly versus CAD/CAM programs that can only adjust per line in the program
- Calculates tooth pass frequency to adapt to low RPM cutters
Remote System Access
The new streamlined browser-based HMI allows users to access TMAC anytime, anywhere, and from any network connected device (including smart phones).
- Remotely view live cutting data from any TMAC system on your network
- View all TMAC data, change job or system parameters, or access the data viewer to analyze historical cutting data from any location
- Multiple users can be logged in simultaneously (with assigned permissions)
Multi Channel Monitoring
Multiple sensor channels can be monitored simultaneously
For instance, you can monitor power, vibration and coolant for a specific tool and section at the same time, and have unique limits for each sensor and channel.
- Create multiple custom views to look at monitoring data in different ways
- View up to 4 monitoring channels in a single view
- Toggle between custom views with the touch of a button
- Change background color to easily identify TMAC systems
- 1 Channel
- 2 Channels
- 3 Channels
- 4 Channels
SENSORS
TMAC has multiple integrated sensor options for total machine condition monitoring.
- Power, vibration and strain sensors can all be used to measure tool wear
- Other peripheral sensors can be installed and monitored by TMAC including spindle speed, coolant flow, and coolant pressure
- GE P11TF12 Compliant
- Power
- Vibration
- STRAIN (Force)
- Coolant Flow
- Coolant Pressure
- Spindle Speed
POWER TRANSDUCER
- Multi-range power sensor measures the power load on the tool to determine wear
HIGH PRECISION POWER
- 24-bit high precision power sensor for monitoring low power cuts
VIBRATION
- Capable of measuring vibration to 22 KHZ, with adjustable sensitivity
- Used for tool wear and breakage detection, and bearing analysis
- Built in temperature sensor
STRAIN (FORCE)
- A strain gauge sensor is embedded in a tool holder to measure the force, to determine tool wear
- Ideal for micro-tools
- Includes built in temperature sensor
COOLANT FLOW
- Available for a wide variety of coolant flow and pressure levels
COOLANT PRESSURE
- Measures coolant pressure in real time
- Allows graphing of all data
- Alarms if out of specification
SPINDLE SPEED
- Accepts input from a spindle encoder or proximity switch to accurately measure spindle speed independent of the CNC control
High Speed Data Processing
The CNC control does not have enough processing power for value-added systems like tool monitoring. For this reason, the TMAC system consists of its own dedicated high-speed processor that handles all communication between TMAC, the sensors, and the CNC control.
- TMAC can monitor multiple sensors simultaneously to handle different types of machining challenges and react instantaneously to changing conditions
- Stores all job information and associated learned and monitored data for easy access and repeatability of cutting programs
- TMAC stops the machine and alarms immediately if there is a problem
- The TMAC processor has a built-in web server to allow remote configuration and monitoring from any network connected device (including smart phones)
- Jobs are stored locally on the TMAC processor so they are always available even when no user interface is connected
- Data is relational and can be exported to other systems
Bearing Analysis
T-mac For Macbook
TMAC monitors spindle bearing health!
A vibration sensor can be attached to the spindle, hardwired to TMAC, with the bearing analysis initiated in the CNC part program.

INTRODUCING TMAC VERSION 3.0!
Caron Engineering's new adaptive tool monitoring system has a browser based user-interface for remote access to live monitoring and system control from any network connected device. Check out all the new features of TMAC 3.0! (Short Video)
Optimize Machine Tool Cutting
TMAC uses high-resolution sensor data to measure tool wear in real-time. Through direct interfacing with the CNC control, TMAC makes automatic and instantaneous corrective adjustments during cutting, without the need for human intervention.
TMAC maximizes your investment in the entire machining process through optimization and the elimination of downtime, resulting in more profitability.
Real-Time Tool Wear Detection
TMAC measures tool wear and detects breakage in real-time by monitoring true spindle motor power. TMAC learns the optimum power for each tool and cutting section, and compares it to the user defined limits to calculate wear as the tool is cutting. It operates on the principle that the power required to cut a part increases as the tool's cutting edges deteriorate.
- Monitors and reacts to tool wear in real-time
- Uses multi-range sensors with auto-scaling display sensitivity
- Prevents tool breakage and lowers scrap rate
- Reduces the cost of consumable tooling
- Provides valuable information about the cutting process
- Stops the machine instantly in the event of tool breakage
TMAC learns the peak power and area under the curve of the cutting tool and can detect tool wear by monitoring these parameters.
- Auto-Scaling Display
- Fixed Limits
- Work (Area Under the Curve)
AUTO-SCALING DISPLAY
TMAC learns the cut and automatically scales the display to the ideal monitoring range, for optimum sensor resolution.
FIXED LIMITS
- TMAC learns the peak power of the cutting tool
- Alarms can be set for extreme (red), wear (yellow), and undercut (blue) per tool
- TMAC will finish the current cut when a wear limit is reached and safely expire the tool after cutting
- TMAC will immediately stop the machine and retract the tool when an extreme limit is reached
- Undercut limits can be set to alarm if not enough power was achieved based on the learned value for the cut
WORK PERCENTAGE (Area Under the Curve)
- With work, TMAC is measuring POWER OVER TIME to calculate the total power consumed over the duration of the cut
- As the tool gets dull, more power is used, so the area under the curve will increase and eventually reach a wear limit indicating a tool change is required
Reduce Cycle Time with Adaptive Control
CNC machines are typically programmed for the safest feed rates to accommodate the worst machining and material conditions.
TMAC adaptive control learns the optimum power for each tool and continuously maintains a constant tool load by automatically adjusting the feed rate in real-time. The result? Decreased cycle time, longer cutter life, and more machine uptime, especially with difficult to machine materials.
- Typical cycle time savings of 20 – 60%
- Allows tools to run at optimum feed rates
- Adjusts to variations in material, tooling, and depth of cut
- Excellent for unattended/lights-out operation
- Adjusts feed rates smoothly versus CAD/CAM programs that can only adjust per line in the program
- Calculates tooth pass frequency to adapt to low RPM cutters
Remote System Access
The new streamlined browser-based HMI allows users to access TMAC anytime, anywhere, and from any network connected device (including smart phones).
- Remotely view live cutting data from any TMAC system on your network
- View all TMAC data, change job or system parameters, or access the data viewer to analyze historical cutting data from any location
- Multiple users can be logged in simultaneously (with assigned permissions)
Multi Channel Monitoring
Multiple sensor channels can be monitored simultaneously
For instance, you can monitor power, vibration and coolant for a specific tool and section at the same time, and have unique limits for each sensor and channel.
- Create multiple custom views to look at monitoring data in different ways
- View up to 4 monitoring channels in a single view
- Toggle between custom views with the touch of a button
- Change background color to easily identify TMAC systems
- 1 Channel
- 2 Channels
- 3 Channels
- 4 Channels
SENSORS
TMAC has multiple integrated sensor options for total machine condition monitoring.
- Power, vibration and strain sensors can all be used to measure tool wear
- Other peripheral sensors can be installed and monitored by TMAC including spindle speed, coolant flow, and coolant pressure
- GE P11TF12 Compliant
- Power
- Vibration
- STRAIN (Force)
- Coolant Flow
- Coolant Pressure
- Spindle Speed
POWER TRANSDUCER
- Multi-range power sensor measures the power load on the tool to determine wear
HIGH PRECISION POWER
- 24-bit high precision power sensor for monitoring low power cuts
VIBRATION
- Capable of measuring vibration to 22 KHZ, with adjustable sensitivity
- Used for tool wear and breakage detection, and bearing analysis
- Built in temperature sensor
STRAIN (FORCE)
- A strain gauge sensor is embedded in a tool holder to measure the force, to determine tool wear
- Ideal for micro-tools
- Includes built in temperature sensor
COOLANT FLOW
- Available for a wide variety of coolant flow and pressure levels
COOLANT PRESSURE
- Measures coolant pressure in real time
- Allows graphing of all data
- Alarms if out of specification
SPINDLE SPEED
- Accepts input from a spindle encoder or proximity switch to accurately measure spindle speed independent of the CNC control
High Speed Data Processing
The CNC control does not have enough processing power for value-added systems like tool monitoring. For this reason, the TMAC system consists of its own dedicated high-speed processor that handles all communication between TMAC, the sensors, and the CNC control.
- TMAC can monitor multiple sensors simultaneously to handle different types of machining challenges and react instantaneously to changing conditions
- Stores all job information and associated learned and monitored data for easy access and repeatability of cutting programs
- TMAC stops the machine and alarms immediately if there is a problem
- The TMAC processor has a built-in web server to allow remote configuration and monitoring from any network connected device (including smart phones)
- Jobs are stored locally on the TMAC processor so they are always available even when no user interface is connected
- Data is relational and can be exported to other systems
Bearing Analysis
T-mac For Macbook
TMAC monitors spindle bearing health!
A vibration sensor can be attached to the spindle, hardwired to TMAC, with the bearing analysis initiated in the CNC part program.
- Results displayed within 5 seconds
- Reports are saved for analysis and trending
- Trend data can be used to establish maintenance requirements
The vibration signal is analyzed for acceleration to detect the health of the bearings, and velocity to detect misalignment, imbalance, and looseness.
Data Viewer and Event Log
T-mac Download For Mac
View the details of any cut, with pan and zoom options for a closer look!
- All monitored data and events are stored and can be exported in various formats for analysis
- Data files can be opened simultaneously to view graphical differences
- Cutting data files can be overlaid to compare cuts
- CNC position data allows the user to inspect the CNC axis positions, program line number, and spindle RPM to interrogate alarms and anomalies at any point in the cut
- Displays detailed information for all events (starts, stops, alarms, etc.)
- Custom events can be created to call out specific points in the cutting operation
- User can apply custom filters to view, sort, and export events for analysis
- Compliant
Advanced Features and Benefits
- Universal interface easily adapts to CNC controls
- Automatic real-time data graphing
- Increased machine tool utilization with less downtime
- Programmable to call a redundant tool when a wear limit is reached (control dependent)
- Easily monitors tapping cycles
- Eliminates air cutting using the approach feed rate feature
- Seamless communication with third party OEE software via the industry standard MTConnect protocol
Download Tmac For Mac
- Supervisors can have special privileges for advanced editing
- Operators can be limited to what they can change
- Remote users with more experience can change critical parameters
- Anyone can view historical data any time